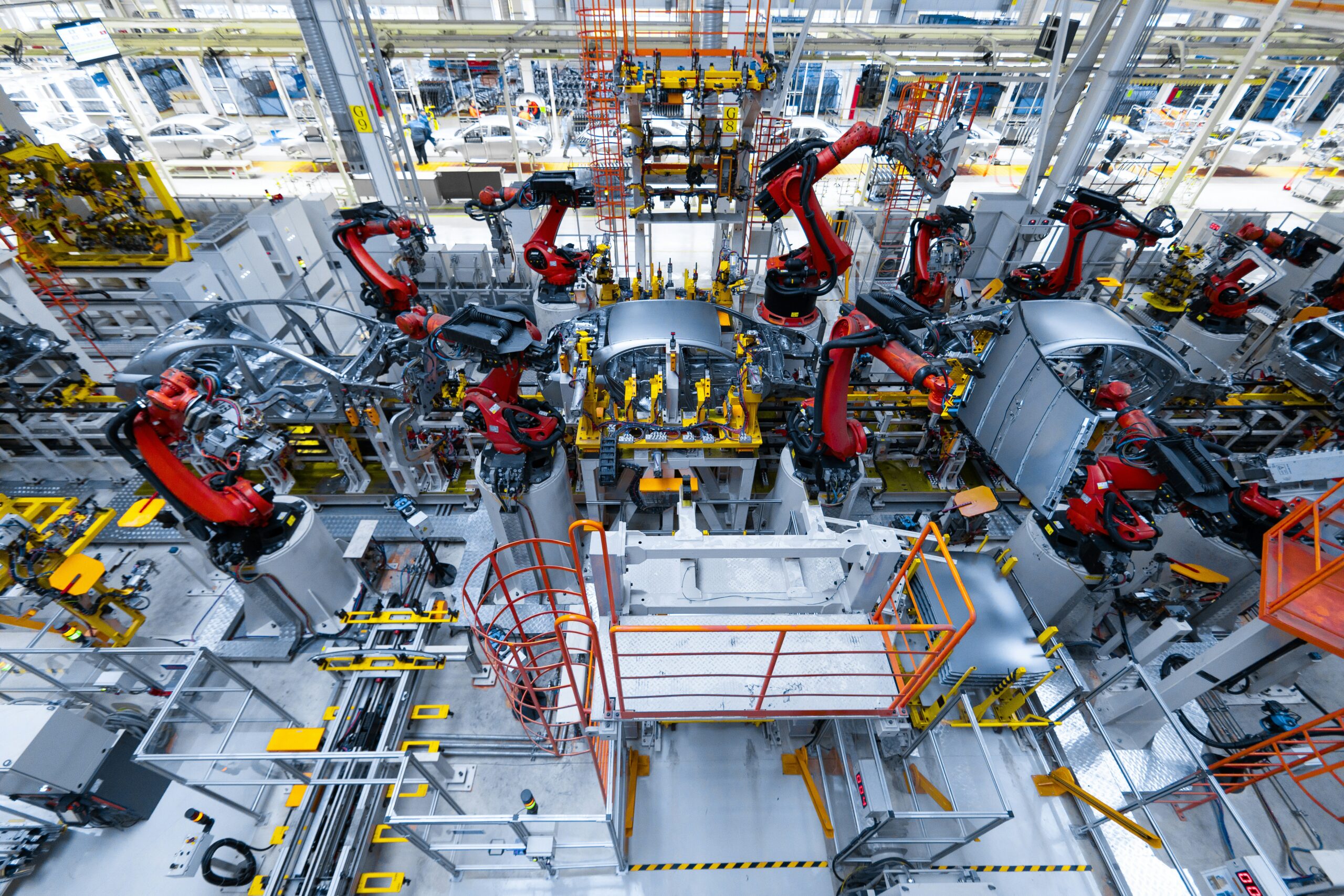
The future of manufacturing doesn’t start with high-tech machinery alone. It begins by understanding how things were built decades ago. Traditional manufacturing methods were more than labor—they were built on skill, patience, and craft. Those values are more relevant today than ever.
In the rush to automate and digitize, many forget the core principles that once drove innovation. The past offers a roadmap. From the workshop floors of the early 1900s to World War II factories, old-school production holds critical lessons. Respect for materials, process control, and worker precision-shaped reliability. These ideas remain essential, even in a digital age.
Craftsmanship Fuels Modern Innovation
Machines are faster, smarter, and more efficient. But they still rely on one thing—human ingenuity. The best innovation in production does not replace craftsmanship; rather, it complements it. It builds on it.
Skilled labor was once passed down through apprenticeships. Workers took pride in every piece made. This mindset helped reduce waste and improve the quality of output. Today, many manufacturers reintroduce hands-on training. It improves both skill and morale. Robots may handle repetition, but they cannot replace the care and attention that go into every weld or assembly.
Industrial Evolution Meets Smart Technology
We are in the middle of the fourth industrial revolution. It’s all about connectivity, data, and AI-powered tools. But what drives this shift? It’s not just technology. It’s the push to be better, cleaner, and more efficient.
That drive existed long ago as well. Early factories introduced belts and pulleys to increase speed. Later came steam engines and electric motors. Now, smart factory solutions use sensors and automation. Yet, they still aim for the same goals: save time, cut costs, and improve quality.
Smart machines learn patterns, correct errors, and predict failures. They keep things running smoothly. But these tools become more powerful when guided by real-world experience. This blend of old wisdom and new tech defines the modern production line.
Sustainable Manufacturing Rooted in the Past
Before mass production, factories were local. Materials were sourced nearby. Waste was rare and not tolerated. That mindset was practical and green before it became a trend.
Today’s focus on sustainable manufacturing borrows from those early habits. Companies now design for recyclability. They reduce emissions and reuse scraps—solar panels power workshops. Water is recycled on-site. These aren’t just tech upgrades. They reflect old lessons: use what you need, waste nothing.
Brands that honor this balance build more than products. They build trust. Customers notice when a company cares about how it creates, not just what it sells.
Human-Centered Workflows Still Matter
Some things machines can’t replicate—like problem-solving, decision-making, and creativity. That’s why the best future of manufacturing puts people first. It combines machine speed with human skill.
Factories today aim for lean production. Every step should add value. This idea is connected to early systems, such as the Toyota Production System. Workers on the floor were empowered to stop the line. That respect for people built better workflows. Modern automation should do the same.
Augmented reality enables workers to view instructions in real-time. Collaborative robots (cobots) assist, not replace. Ergonomic tools prevent injuries. These tools ensure human effort stays valuable.
Agility Comes From Historical Foundations
Adaptability drives success. During wartime, factories shifted from producing cars to manufacturing tanks in just a matter of weeks. That flexibility was possible because systems were modular and teams were well-trained.
Today, the industrial evolution continues. Supply chains break, materials run short, and demand shifts overnight. Agile factories respond by learning from their past experiences. They use modular designs, flexible teams, and real-time data.
Factories now switch product lines in days, not weeks. They adopt just-in-time production and keep smaller inventories. These ideas have roots in past eras where efficiency was a matter of survival, not just a strategy.
Legacy Systems Still Offer Value
Many modern plants run on older infrastructure. Instead of tearing it down, many update it with new tech. Legacy machines can be equipped with sensors and controllers to enhance their functionality and performance. This hybrid approach saves money and reduces downtime.
Why reinvent everything? Older systems were built to last. Steel frames, cast-iron parts, and mechanical precision still hold their value. When paired with modern software, they become even more powerful. The future of manufacturing includes the past, not as history but as hardware.
Workforce Knowledge Must Be Preserved
One of the greatest risks today is losing tribal knowledge. As older workers retire, their experience disappears. That’s a problem no AI can fix. Companies must capture this knowledge before it vanishes.
Mentorship, documentation, and video training help transfer wisdom. Encouraging mixed-age teams improves communication and retention. When senior workers guide younger ones, both sides benefit.
Technology changes fast. However, the wisdom of knowing how to make things right the first time never grows old. Keeping that alive is not just smart; it’s essential. It’s vital for progress.
The Power of Blending Old and New
A factory of the future doesn’t mean robots everywhere. It means using every tool available—manual, digital, or mechanical. From antique lathes to AI dashboards, every part plays a role.
Leaders in the field know this. They invest in both new machinery and employee education. Leaders don’t chase trends and build systems with purpose. That includes honoring what worked before and adapting it to now.
The most successful companies understand this truth: progress doesn’t erase the past. It builds on it.
Looking Ahead With Eyes on the Past
As we move toward cleaner, faster, and smarter ways to build, we must not forget where it all started. From blacksmith shops to smart factories, every leap forward echoes an earlier one.
The future of manufacturing thrives when tradition meets innovation. Companies that blend both will lead tomorrow’s industry, not with just speed or cost, but with care, precision, and pride.